[敬邀參加] MITxNCTU-Beyond Future Mobility未來綠能及智慧行動車論壇/暑期工作坊
交通大學與MIT Media Lab即將於八月份於台北空總基地舉辦"未來綠能及智慧行動車論壇及工作坊",歡迎本校電機學院師生到場與各界交流(參加8/11單日論壇或組隊報名全程工作坊皆可),以下為本活動相關資訊連結,敬邀學生及教師參加。
為提升台灣創新之國際能見度,NCTU與MIT Media Lab合作舉辦本系列活動(8/11論壇及8/12~8/15工作坊),期望結合國際視野及在地參與,發展出未來人類綠能及智慧行動車創新示範案例!
8/11第一日趨勢論壇(英文進行),除報名參加工作坊之團隊外,特別開放部分名額予各界人士參與,歡迎您前來現場交流!
★ 活動時間:104年8月11日(二)~8月15日(六)
★ 活動地點:TAF空總創新基地(台北市仁愛路三段55號)
★ 報名期間:即日起至104年8月3日(一)13:00止,經資格審核後,8月4日15:00於活動網頁公布錄取名單
★ 活動議程:8/11第一日論壇報名:http://rd.nctu.edu.tw/ic_news&dbid=T6DV
8/11~8/15 全程活動(論壇+工作坊)報名:http://rd.nctu.edu.tw/ic_news&dbid=OK7Q
★ 指導單位:教育部、經濟部
★ 主辦單位:MIT Media Lab、國立交通大學
★ 聯絡窗口:2015mitworkshoptw@gmail.com
【工作坊執行方式】
透過第一日科技分享及論壇帶出議題發想概念,參加團隊選擇想進行的主題,從概念發想、實作輔導到成果產出,於最後一日Demo Day展出,由MIT專家群與台灣產學界前輩共同選出優勝隊伍。優勝隊伍須配合後續主辦單位成果展示,並有機會被選送赴MIT Media Lab進行短期進修/學術交流。
活動現場備有Maker Space,並免費提供以下設備供實作prototype:3D列印機/雷射切割機/拋模機/烙鐵/銼刀
【工作坊主題】
IT 資訊科技
包含影像處理(Image Processing)、通訊(Communication)、自動控制(Automatic Control)、大數據管理(Management/Big Data)、雲端科技(Cloud Computing)、新媒體(New Media)
IC/SOC/Sensing 積體電路/系統晶片/感測
Transportation 運輸:
包含自動車(Automotive)、追蹤系統(Track System)、航空(Aviation)、無人機(Maritime/UAV)、介面設計(Interface Design)、服務(Service)
Machinery 機械
包含工具(Tools)、設備(Equipment)、系統(System)、機器人(Robotics)、人機互動(Human-Computer Interaction)
Energy Storage and Generation 未來綠能與環境
包含電池(Battery)、燃料電池(Fuel Cell)、未來綠能(Future Green)、永續設計(Sustainable Design)
【活動報名辦法】
報名期間:即日起至104年8月3日13:00止,逾期皆不予受理
報名資格:大專院校師生/實驗室、法人研究機構或成立5年以內的新創公司團隊,需具備基本英文溝通能力
報名方式:需組隊參賽報名,4~6人為一組(恕不受理個人報名),經資格審核後,8月4日15:00於活動網頁公布錄取名單並另由專人email通知
報名費用:全程免費+供午晚餐
【活動網頁】
http://rd.nctu.edu.tw/ic_news&dbid=OK7Q
【報名網址】
http://goo.gl/forms/XAmecZu0tL
【聯絡人】
許萬龍 / David Hsu, Ph.D.
國立交通大學 產學運籌中心 執行長 & 創業育成中心 執行長
Tel: 03-5131385
[email protected]
davidhsu@mail.nctu.edu.tw
同時也有2部Youtube影片,追蹤數超過0的網紅channelvtc,也在其Youtube影片中提到,VTC專家(IVE汽車工程系講師 馮敏強) 解說電動車售價昂貴,在港普及化仍需一段時間。 IVE汽車工程系講師 馮敏強接受訪問,指出電動車的鋰電池成本高,令車價高企,而車廠亦暫時未能開發其他電池材料取代鋰電池。 (短片由香港寛頻電視新聞部 提供)...
automotive battery cell 在 channelvtc Youtube 的評價
VTC專家(IVE汽車工程系講師 馮敏強) 解說電動車售價昂貴,在港普及化仍需一段時間。
IVE汽車工程系講師 馮敏強接受訪問,指出電動車的鋰電池成本高,令車價高企,而車廠亦暫時未能開發其他電池材料取代鋰電池。
(短片由香港寛頻電視新聞部 提供)

automotive battery cell 在 CarDebuts Youtube 的評價
The BMW Group continues to expand its electro-mobility activities. In conjunction with its partner, Brilliance China Automotive Holdings Ltd., the BMW Group opened a new “High-Voltage Battery Centre” in Shenyang, China today. The battery factory will supply the nearby Dadong plant, which is operated by the BMW Brilliance Automotive (BBA) joint venture and will produce the BMW 5 Series Plug-in Hybrid for the local market.
Oliver Zipse, member of the Board of Management of BMW AG, responsible for Production: “The innovative High-Voltage Battery Centre in Shenyang is an important step in the BMW Group’s electro-mobility strategy. It is the first battery factory of any premium automotive manufacturer in China and already the third in our production network, after Germany and the US.”
The BMW Group is integrating its battery factories into the existing international production network. Oliver Zipse: “By 2025, we expect our electrified BMW and MINI models to account for between 15 and 25 per cent of global sales. This adds up to several hundred thousand vehicles per year. It therefore makes sense for us to integrate electro-mobility into the existing production system.” Doing so will enable the BMW Group to respond flexibly to demand for electrified models.
Competitive edge through in-house know-how
Alongside the electric motor, the high-voltage battery is a central element of partially and fully-electrified vehicles. In-house production gives the BMW Group a decisive competitive advantage by securing know-how in new technologies, gaining key systems expertise and leveraging cost benefits. The company already produces electrified vehicles at ten locations worldwide. The high-voltage batteries needed for these models come from the BMW Group plants in Dingolfing, Spartanburg and now also Shenyang. The Dingolfing plant will play a leading role within the network as the centre of competence for electric drive systems.
From cell to high-voltage battery
Production of high-voltage batteries is divided into two production stages. First, in a highly-automated process, supplied lithium-ion cells, which are about the size of a paperback book, are checked and then combined into a larger unit, the so-called battery module.
The battery modules are then mounted together with the connections, control units and cooling units in an aluminium housing. The size and shape of the aluminium housing, as well as the number of battery modules used, depends on the vehicle variant. In this way, a perfectly adapted "battery pack" or high-voltage battery is created.
This combination of standardised battery modules and housings flexibly adapted to the vehicle has several advantages: It ensures uniform properties and quality standards in the production of high-voltage batteries. The modular design of the high-voltage batteries also forms the basis for a wide variety of electric drive variants. Last but not least, this modular concept is a requirement for responding quickly to customer demand and leveraging cost benefits.
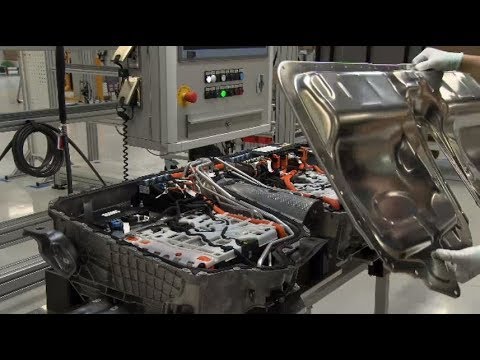